Batching plants usually mix each component individually by its weight. However, these properties can be altered to produce different qualities and grades of concrete. Different regions require different classes of concrete for construction. Read on as we dive into how cement bathing plant works.
If you didn’t already know, there are two types of concrete plants. These being the dry mix plant and the wet mix plant. The names already suggest the dry concrete plant whips up a dry mix before dispatching. The materials are firstly weighed and then placed into the mixer. Water is added and during the delivery time, the mixture undergoes the mixing process.
In the case of a wet concrete plant, the materials are firstly weighed and individually added into the unit. However, the unit mixes the materials and dispatches them into either a pumping or transit unit. These are also referred to as central mix plants and provide users with a more consistent concrete mixture.
The control unit on the plant is fitted with a specially designed computer-aided software which maintains a high standard. Both dry or wet concrete plants usually come in tow forms, these being either mobile or stationary. Stationary plants are usually desired since they allow contractors to produce from one location. Stationary plants usually have an advantage over mobile plants since they have a larger carrying capacity.
On the other hand, mobile plants are very reliable, accurate, productive and they are designed to work for many years to come. These plants work using the following principle:
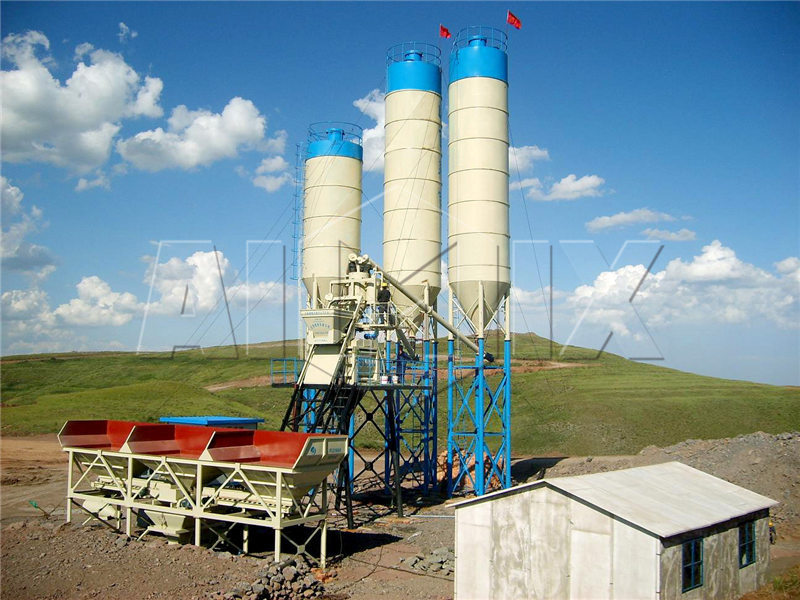
* Aggregate Feeding – Sand and aggregates are fed into the feeder bins.
* Powder Feeding – This usually refers to the additives, fly ash, and cement. All of these are important binding elements of a good cement slurry.
* Water – Water ensures that all components are evenly mixed and bound together. However, specific quantities are required for special consistency.
* Storage And Conveyance – Both revolve around storing fly ash, cement, and other useful additives. Plants are required to store different quantities of each as they transfer smaller amounts to the weighing hoppers.
* Control System – This is crucial and important for machines. Control systems contribute to the fast and accurate operations of machines.
This concrete batching plants process begins from the moment the aggregates are fed to the bins. Depending on the size, aggregates are stored into their own bins. The aggregates are then weighed using the control panel where they are transferred directly into the mixing unit.
Located just above the mixing unit are the hoppers that are designed to weigh the cement, water, and additives. After weighing the cement, it is then transferred to the mixing unit. However, cement reaches the hopper via the screw conveyor.
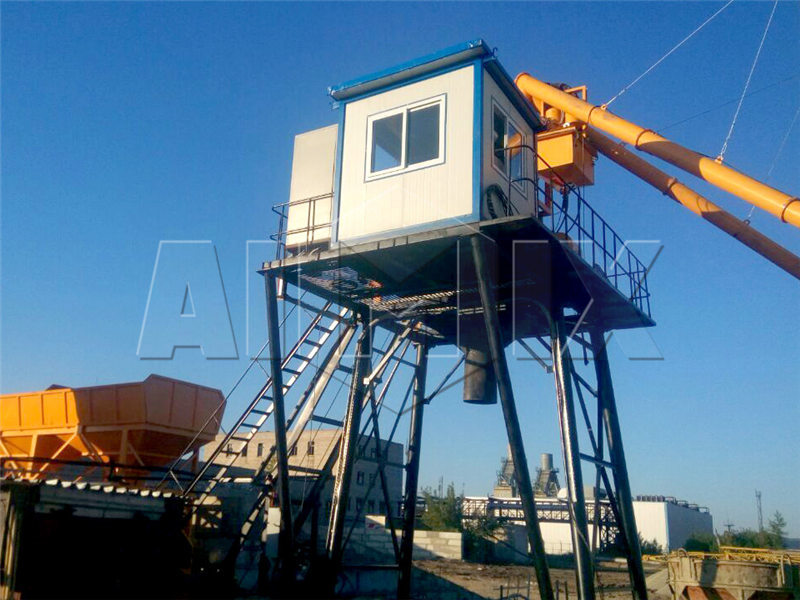
Water is then pumped into the weigh hopper and a desired mixing time is set. Upon completion, the contents are discharged into a pump or transit mixer.
As we conclude we have just looked at how cement concrete batch mix plant works. While the above process may seem simple, it is carried out in a safe and systematic manner. Each step of the process is run for a set time to produce the desired quality of concrete. These plants are essentially useful to contractors since they can always have fresh concrete ready in no time.